About STEELO
When Peace of Mind Matters.
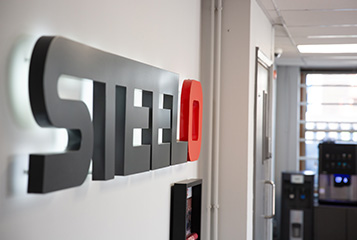
Steelo understands that when you order structural steel products, you want more than just for the product to turn up. You need the product to be on time, to specification, and built to last.
We have forged our reputation on our ability to design, produce and deliver the highest quality product, to the highest standard. We’re proud to have been recognised as the Best Structural Steel Fabricator – London by Build Construction & Engineering for three consecutive years: 2022, 2023, and 2024.
Arek Szurczak,
Managing Director
Steelo Team
We’re the ones delivering excellent customer satisfaction, greeting you on Monday morning, solving complex designs, meeting your deadlines, and helping you deliver projects on time. Behind the scenes, our back-office designers bring your vision to life in 3D. Our welders, cutters, and painters meticulously craft your structures to exact specifications. And when the work is done, it’s our drivers who ensure on-time, safe delivery to your site, every time.
#WeAreSteelo.